Cet article de Jennifer Heathcote, vice-présidente du développement commercial de GEW, Inc, explique comment les professionnels peuvent gérer la quantification de l’énergie émise par les sources de polymérisation UV.
- Comprendre et quantifier l'énergie émise par les sources de polymérisation UV
- Qu’est-ce qui est mesuré et comment est-il mesuré ?
- Différences de sortie spectrale pour les sources de polymérisation au mercure et aux LED UV
- Comment les diagrammes de sortie spectrale/irradiance sont-ils utilisés dans la pratique ?
- Pénétration de longueur d'onde pour les systèmes de polymérisation à l'arc d'électrode et aux LED UV
- Evolution de la chimie UV
Comprendre et quantifier l’énergie émise par les sources de polymérisation UV
Dans les processus de durcissement par UV, l’énergie ultraviolette émise par la vapeur de mercure et les têtes de lampes UV LED est caractérisée par l’irradiance, la densité d’énergie, la puissance spectrale et l’irradiance spectrale. Comprendre ces éléments et la manière dont ils sont quantifiés permet aux utilisateurs de mieux adapter les sources de polymérisation UV aux besoins des formulations, des processus et de la manipulation des matériaux. Lorsque la sortie UV est adaptée de manière appropriée, une photopolymérisation réussie et efficace se produit aux vitesses de ligne souhaitées et aux distances de travail ou de décalage requises. De plus, lorsque les fenêtres de fonctionnement pour l’irradiation et la densité énergétique sont maintenues au fil du temps, un produit de qualité est produit de manière cohérente et reproductible.
Les éléments couramment référencés qui caractérisent la production d’UV comprennent :
- Irradiance (W/cm2) – Il s’agit de la puissance radiante arrivant sur une surface de polymérisation sous tous les angles vers l’avant, par unité de surface.1 Elle est généralement indiquée comme l’irradiance effective sur une bande passante définie et est plus significative lorsqu’elle est référencée à une plage de fonctionnement spécifiée. distance pour le système de durcissement UV mesuré.
- Densité d’énergie (J/cm2) – Il s’agit de l’énergie rayonnante arrivant sur une surface de polymérisation par unité de surface.1 Elle est généralement rapportée comme la densité d’énergie effective sur une bande passante définie. Bien qu’il puisse être considéré comme l’irradiation maximale multipliée par le temps, le calcul de la densité énergétique est un peu plus complexe pour la plupart des configurations de séchage UV et des installations de chaînes de fabrication. Ceci est discuté plus loin dans l’article.
- Sortie spectrale – Il s’agit de la puissance radiante (W) d’une lampe par rapport à la longueur d’onde (nm). Elle est exprimée en W/nm ou W/10nm.1
- Irradiance spectrale – Il s’agit de la puissance radiante d’une lampe par unité de surface (W/cm2) par rapport à la longueur d’onde (nm). En d’autres termes, il s’agit de l’irradiance par longueur d’onde. Elle est exprimée en W/cm2/nm.
L’irradiance, la densité énergétique, la puissance spectrale et l’irradiance spectrale varient selon le type de lampe, le fournisseur de lampe, la conception de la tête de lampe, la puissance électrique appliquée et les heures de fonctionnement. De plus, l’ampleur de l’irradiance et de la densité d’énergie qui atteignent finalement la surface de polymérisation sont fortement influencées par la manière dont les systèmes sont intégrés dans les lignes de fabrication et par la manière dont les systèmes sont entretenus après la mise en service. Heureusement, une fois qu’un système de durcissement UV est adapté à une formulation et correctement intégré dans une ligne de production, le processus de durcissement est incroyablement reproductible et peut être contrôlé grâce à une mesure périodique de l’irradiance et de la densité d’énergie ainsi qu’à une maintenance régulière du système.
Irradiance
L’irradiance (W/cm2) est la puissance d’un système de durcissement UV à un instant donné par unité de surface et est souvent appelée intensité de la lampe. Puisque les unités de W/cm2 sont équivalentes à J/cm2/s, l’irradiance peut être considérée comme la vitesse à laquelle la densité d’énergie (J/cm2) est délivrée à la surface durcie. En d’autres termes, l’irradiance est le débit de dose.
Dans tout l’univers, les ondes électromagnétiques d’énergie divergent les unes des autres à mesure qu’elles s’éloignent de leur source émettrice respective. À mesure que les ondes divergent avec la distance, l’ampleur de l’irradiance correspondante diminue également. Selon la loi du carré inverse, l’irradiance est inversement proportionnelle au carré de la distance parcourue. En conséquence, si l’irradiance à une distance définie d’une source émettrice est connue, l’irradiance à une seconde distance peut être calculée à l’aide de la loi du carré inverse.
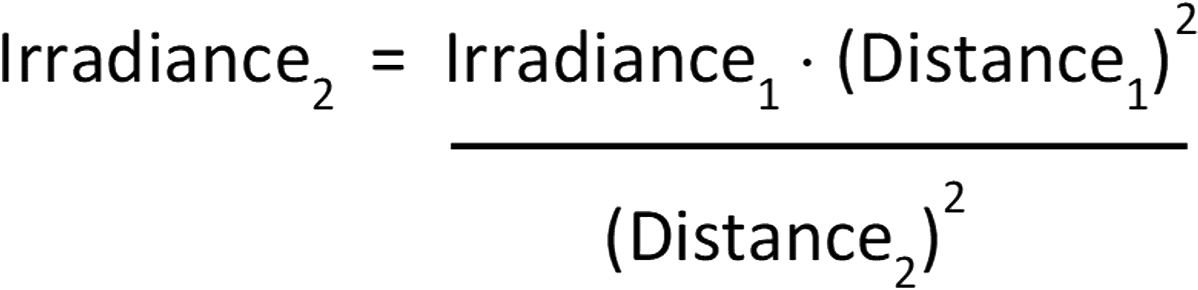
À proximité des têtes de lampes à séchage UV, l’irradiance n’est qu’approximativement proportionnelle à la loi du carré inverse. En effet, les ingénieurs intègrent des réflecteurs et d’autres éléments optiques dans la conception des têtes de lampe pour rediriger les rayons UV sur de courtes distances et minimiser la propagation naturelle de la lumière. De plus, dans le cas des têtes de lampes UV LED, les sources émettrices sont composées de nombreuses petites diodes, chaque diode servant de source ponctuelle distincte de lumière rayonnée. Une courte distance de déplacement est nécessaire pour que les ondes émises par de nombreuses sources ponctuelles LED se mélangent uniformément et forment finalement une source unique de rayonnement uniforme. Les réflecteurs, les optiques et l’utilisation de plusieurs diodes contournent la loi du carré inverse sur de courtes distances des têtes de lampes à polymérisation UV.
Les ingénieurs utilisent des optiques et des réflecteurs pour focaliser ou collimater la sortie des systèmes de durcissement UV. Les optiques et les réflecteurs concentrent les rayons lumineux, ce qui augmente ensuite l’intensité de l’irradiation à la distance de travail prévue ou sert à maintenir une irradiation plus constante sur une plage définie de distances de travail. Pour les lampes à arc à électrodes et à micro-ondes classiques, la zone de concentration focalisée est appelée point focal. À l’inverse, les systèmes LED conventionnels et UV sans point focal ou autre optique entraînent des rayons lumineux divergeant naturellement les uns des autres dès qu’ils sortent de la tête de lampe. Cela inonde la lumière UV sur une surface beaucoup plus large. Le montage d’une tête de lampe de telle sorte que la surface de polymérisation se trouve au-delà du point focal produit un résultat similaire. En général, les systèmes d’inondation, les systèmes montés hors foyer et les systèmes montés à des distances de travail de plus en plus grandes entraînent une diminution de l’irradiation au niveau de la surface de polymérisation.
Pour les lampes à arc à électrodes, l’irradiance est la plus grande au point focal. Pour les systèmes de polymérisation UV-LED, qui n’ont pas de point focal, ainsi que pour les lampes conventionnelles avec un profil Flood, l’irradiance est maximale à proximité de la sortie de la tête de lampe ou de la fenêtre en quartz. En raison des différences technologiques inhérentes, les systèmes de durcissement par LED UV peuvent être conçus pour émettre des valeurs d’irradiation inférieures, similaires ou nettement supérieures à celles des lampes à vapeur de mercure à moyenne pression. Cependant, les systèmes LED UV émettent cet éclairement sur une bande de longueurs d’onde beaucoup plus étroite, ce qui rend difficile la comparaison directe des systèmes de polymérisation conventionnels et LED. Comme indiqué précédemment, les valeurs d’irradiance pour les deux technologies sont fortement influencées par la distance parcourue par la lumière. Par conséquent, la distance de décalage entre une tête de lampe et la surface supérieure d’un outil de mesure UV ou entre une tête de lampe et une surface de polymérisation est importante et doit toujours être notée lors de la configuration et de la tenue des registres.
En plus du fait que l’irradiance dépend des configurations des têtes de lampe, telles que focalisées ou inondées pour les lampes à arc à électrodes et collimatées ou inondées pour les LED UV, l’irradiation émise par un système de durcissement UV augmente et diminue avec les changements correspondants dans la puissance de la lampe et la distance de décalage. À condition que la puissance de la lampe et la position de la tête de lampe par rapport à la surface de durcissement ne changent pas, et en ignorant la dégradation progressive de la lampe au fil du temps, l’irradiance reste constante en chaque point du profil d’irradiation, quelle que soit la vitesse ou la lenteur avec laquelle les bandes, feuilles ou pièces passent ou restent. devant un système de durcissement UV.
En pratique, étant donné que la plupart des processus de durcissement par UV intègrent une certaine forme de manipulation des matériaux ou d’automatisation des têtes de lampe, la surface de durcissement se déplace généralement par rapport à la source émettrice. En conséquence, l’irradiance délivrée à une petite zone mobile sur la surface de polymérisation n’est pas constante pendant la durée d’exposition. Cette exposition dynamique est le résultat de légères variations de la puissance émise, de fluctuations de la distance de travail dues au rebond de la bande ou aux profils de pièces déformés, de retards dans l’actionnement de l’obturateur, d’une surface de durcissement qui passe devant une tête de lampe stationnaire ou d’une tête de lampe qui passe dans devant une surface de durcissement stationnaire. L’exposition dynamique fait référence à tout processus dans lequel la surface durcie subit une irradiation variable pendant la durée de réaction de la formulation.
Imaginez une petite zone sur une bande, une feuille ou une pièce beaucoup plus grande se déplaçant vers, sous et s’éloignant d’une source fixe de durcissement UV. À mesure que la zone sélectionnée se rapproche de la lumière, l’irradiance maximale arrivant dans la zone augmente rapidement. L’irradiance au niveau de la zone continue d’augmenter jusqu’à ce qu’elle atteigne une valeur maximale au point où la zone passe par le point focal ou le centre de la tête de lampe. À mesure que la même petite zone sur la surface de polymérisation s’éloigne du point focal ou du centre de la tête de lampe, l’irradiance maximale arrivant dans la zone diminue rapidement. Les profils d’irradiation UV illustrent graphiquement comment l’irradiation maximale délivrée à une surface durcie varie en fonction du temps. Pour le scénario qui vient d’être décrit, le profil d’irradiance UV ressemble à une courbe en forme de cloche.
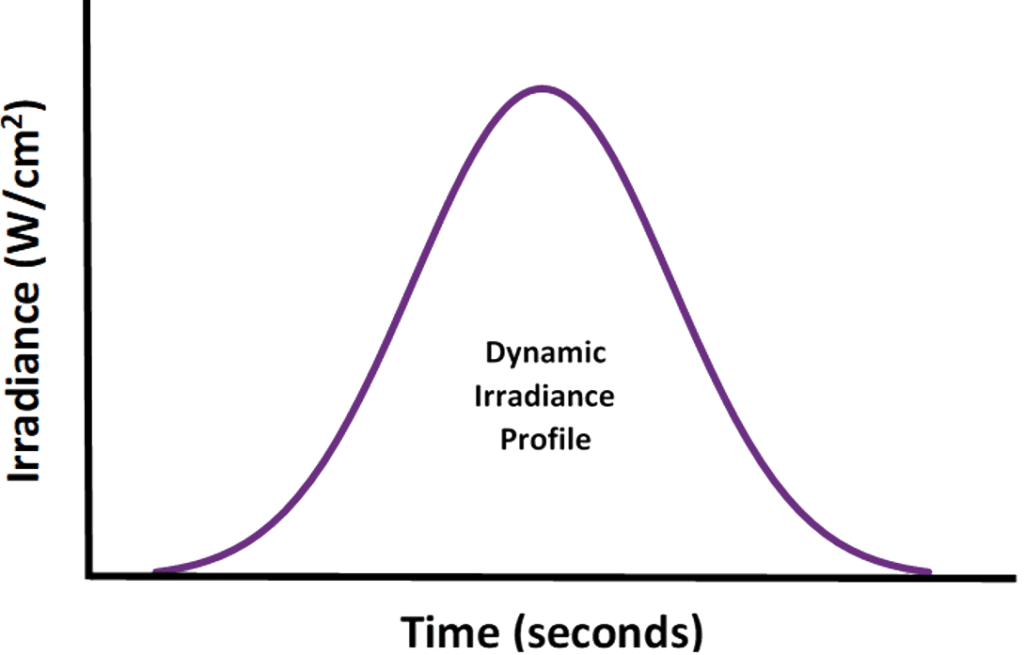
En revanche, l’exposition statique fait référence à tout processus dans lequel la surface durcie subit une irradiation constante pendant tout le temps de réaction de la formulation. Ceci est possible dans les applications de durcissement ponctuel et de zone et avec des chambres de durcissement spécialement conçues. Dans chacun de ces cas, la tête de lampe et la surface de polymérisation ne bougent pas, la totalité de la surface de polymérisation est exposée uniformément tout au long de la réaction et l’énergie UV délivrée est activée et désactivée instantanément. L’exposition statique est représentée par le profil d’irradiation rectangulaire suivant.

Densité énergétique
La densité énergétique (J/cm2) est l’énergie totale délivrée par un système au fil du temps par unité de surface et est souvent appelée dose. Mathématiquement, la densité d’énergie fait partie intégrante de l’irradiation dans le temps et est souvent estimée en multipliant l’irradiation maximale par l’exposition ou le temps de séjour. Cependant, l’estimation par multiplication donne généralement une valeur de densité d’énergie trop élevée car l’irradiation à la surface de polymérisation est rarement statique. Ceci est illustré par les profils d’irradiance statiques et dynamiques suivants où la densité d’énergie est équivalente à l’aire sous la courbe.

Le profil rectangulaire représente une exposition statique où l’irradiation est constante dans le temps. En revanche, le profil en forme de cloche représente une exposition dynamique dans laquelle la surface de polymérisation ou la tête de lampe se déplacent l’une par rapport à l’autre. La surface sous le profil rectangulaire est facilement calculée en multipliant l’irradiation maximale par la durée d’exposition totale. Dans le cas d’une exposition dynamique, la multiplication de l’irradiation maximale, qui se produit au sommet de la courbe en forme de cloche, par la durée d’exposition totale surestime largement la densité énergétique.
La densité énergétique peut être augmentée en augmentant la puissance de la lampe, en ralentissant la vitesse de la ligne, en augmentant le temps de séjour, en ajoutant plus de lampes ou en passant plusieurs fois une surface de polymérisation devant une source de lumière. Bien qu’il existe des exceptions liées à l’atmosphère, à l’intégration et à l’orientation de la lampe, la densité énergétique est peu affectée par la distance de travail pour la plupart des applications. Dans le cas des LED, des lampes plus larges avec des diodes espacées de manière optimale sont également utilisées pour offrir une densité énergétique supplémentaire.
Sortie spectrale et éclairement spectral
La puissance spectrale est la puissance radiante d’une lampe (W) par rapport à la longueur d’onde (nm). La sortie spectrale est exprimée en W/nm ou W/10 nm.1 L’irradiance spectrale est étroitement liée, à savoir l’irradiance par unité de longueur d’onde (W/cm2/nm).1 Les deux sont mesurés à l’aide d’un spectroradiomètre qui est un instrument qui combine les fonctions de un radiomètre et un monochromateur pour mesurer l’irradiance dans des bandes passantes finement divisées.1
Les longueurs d’onde ultraviolettes et visibles sont généralement mesurées en milliardièmes de mètre (0,000000001 m) ou en nanomètre (nm). Pour référence, une feuille de papier a une épaisseur d’environ 100 000 nanomètres. La plage spectrale UV standard ISO2 est définie comme étant de 10 à 400 nm tandis que la plage visible est de 400 à 700 nm. Aux fins du durcissement par UV, les organismes industriels et les experts classent la lumière ultraviolette comme s’étendant entre 200 et 450 nm, entre autres variations. En conséquence, des plages différentes, parfois superposées, sont souvent référencées et utilisées dans la pratique. La meilleure façon d’illustrer et de communiquer la distribution de longueurs d’onde d’une source de durcissement UV ainsi que la puissance relative à travers la distribution consiste à utiliser un graphique de sortie spectrale ou d’irradiance spectrale.
Un graphique de sortie spectrale/irradiance est un graphique linéaire ou à barres avec soit la puissance radiante ou l’irradiance d’un système sur l’axe y et les longueurs d’onde correspondantes sur l’axe x. Le rendement spectral/irradiance est un facteur de type de lampe et est différent pour les lampes à vapeur moyenne pression au mercure, au fer et au gallium ainsi que pour les LED 365, 385, 395 et 405 nm. La sortie spectrale/l’irradiance dépend également des caractéristiques de conception du système mécanique et électrique qui influencent la manière dont la lumière est émise directionnellement par une tête de lampe ; propriétés physiques des réflecteurs, fenêtres et autres éléments ; la puissance à laquelle la lampe est entraînée ; et l’efficacité du système de refroidissement. Le graphique de sortie spectrale/irradiance d’un produit est une spécification fournie par les fournisseurs de lampes et de systèmes. Il est destiné à titre de référence uniquement et n’est pas quelque chose qui est couramment mesuré ou recréé par les utilisateurs de terrain de la technologie. Il est important de noter que la sortie spectrale et l’irradiance spectrale des lampes UV ou LED individuelles diffèrent considérablement de la sortie spectrale et de l’irradiance spectrale du système de durcissement UV une fois que la source a été entièrement intégrée aux autres composants.
La sortie spectrale/irradiance peut être affichée de plusieurs manières, notamment en valeur absolue exprimée en (W/nm) ou (W/cm2/nm) ou en mesures arbitraires, relatives et normalisées (sans unité). Les profils affichent généralement les informations sous forme de graphique linéaire ou à barres, les graphiques à barres intégrant généralement la sortie sur des bandes de 10 nm. L’utilisation de bandes de 10 nm facilite l’interprétation des informations et réduit la difficulté de quantifier les effets des spectres d’émission de raies1. Les graphiques spectraux relatifs et normalisés sont les représentations les plus courantes.
Qu’est-ce qui est mesuré et comment est-il mesuré ?
Alors que le rendement spectral et l’irradiance spectrale sont des spécifications de lampe mesurées à l’aide de spectroradiomètres spécialisés, l’irradiance et la densité d’énergie sont mesurables sur le terrain à l’aide de radiomètres portables moins coûteux et disponibles dans le commerce.
Dans certains cas, comme avec l’option mUVm de GEW, la surveillance UV peut être directement intégrée au porte-lampe et aux commandes du système correspondantes. Chaque fois que l’irradiation et la densité d’énergie sont mesurées avec un radiomètre, les lectures sont toujours relatives à une source d’étalonnage standard choisie par le fournisseur du radiomètre. Les valeurs mesurées sur le terrain ne sont jamais des valeurs absolues. Il s’agit plutôt de valeurs relatives directement corrélées à la source d’étalonnage d’usine. Cela implique que différents compteurs ont tendance à indiquer des valeurs différentes.
En conséquence, les radiomètres sont mieux utilisés comme dispositifs de contrôle de processus où le même compteur et le même protocole de mesure sont systématiquement utilisés pour surveiller la production d’UV au fil du temps pour un laboratoire ou une ligne de production donnée. Lorsque les valeurs mesurées d’irradiation ou de densité d’énergie tombent en dessous des niveaux minimaux, des ajustements du système peuvent être effectués pour ramener le processus sous contrôle. Il convient de noter que les radiomètres sont conçus pour mesurer les lampes à vapeur de mercure ou les LED. Le même type de compteur ne mesure pas les deux catégories de sources émettrices.
Les radiomètres échantillonnent l’irradiance d’un système plusieurs fois par seconde sur une plage de longueurs d’onde spécifiée. La fréquence à laquelle les échantillons sont enregistrés est appelée taux d’échantillonnage. L’échantillonnage se produit au fil du temps lorsque le compteur passe devant une ou plusieurs sources lumineuses. L’irradiance maximale du système est signalée comme la valeur la plus élevée dans l’ensemble des points de données échantillonnés. Les valeurs d’irradiance maximale distinctes mesurées sur différentes bandes passantes telles que UVC, UVB, UVA et UVV ne sont pas additives car la définition de l’irradiance maximale est la plus grande valeur mesurée à une longueur d’onde donnée ou sur une plage de longueurs d’onde. La plage de longueurs d’onde sur laquelle les valeurs d’irradiance sont échantillonnées est une spécification fixe du compteur et dépend de la sensibilité et de la plage des photodiodes du compteur.
L’ensemble complet des points de données d’irradiance maximale collectés lorsqu’un radiomètre passe devant une source UV forme le profil d’irradiance. L’intégration de ce profil, qui est l’aire sous la courbe, correspond à la densité énergétique. Pour les expositions dynamiques telles que le profil en forme de cloche dans l’image suivante, la densité d’énergie est déterminée en calculant et en ajoutant de nombreuses zones plus petites. L’aire de chaque petit rectangle est déterminée en multipliant chaque point de données sur le profil par le temps écoulé entre les points de données. Il s’agit d’une méthode bien établie d’intégration de zones sous des profils non linéaires et c’est la raison pour laquelle les radiomètres qui mesurent la densité d’énergie sont appelés radiomètres intégrateurs.

Différences de sortie spectrale pour les sources de polymérisation au mercure et aux LED UV
La sortie des systèmes de durcissement UV conventionnels couvre les longueurs d’onde ultraviolettes (UV), visibles et infrarouges. Pour cette raison, les lampes UV à arc et à micro-ondes sont considérées comme à large bande ou à large spectre. La production des systèmes standard à vapeur de mercure à moyenne pression couvre l’ultraviolet, le visible et l’infrarouge dans des proportions à peu près égales. La distribution spectrale dans la bande UV peut être légèrement modifiée en ajoutant de petites quantités de dopants métalliques tels que le fer (Fe), le gallium (Ga), le plomb (Pb), l’étain (Sn), le bismuth (Bi) ou l’indium (In). . Les lampes avec des métaux ajoutés au mélange de mercure de base et de gaz inerte sont généralement appelées lampes dopées, additives ou aux halogénures métalliques.
En revanche, la sortie des LED UV est concentrée dans la bande ultraviolette avec une certaine sortie visible et pas d’infrarouge. Les LED UV émettent de la lumière lorsque le courant traverse un ensemble de diodes à semi-conducteurs fabriquées. De nombreuses diodes discrètes sont regroupées dans une seule rangée, une série de rangées et de colonnes ou une autre configuration. La disposition des diodes forme la longueur et la largeur de la source d’émission. La sortie spectrale des systèmes LED UV est basée sur une science des matériaux complexe où des centaines ou des milliers de diodes sont cultivées couche par couche sur des tranches dans des salles blanches, puis découpées ou extraites individuellement après la fabrication. Les longueurs d’onde émises par une LED ne peuvent pas être modifiées ou ajustées après la production ; cependant, l’ampleur de son irradiance est hautement réglable pour un système de durcissement donné et a généralement une plus grande portée que les lampes à arc à électrodes et à micro-ondes.
Le tableau d’irradiation spectrale suivant illustre la relation générale entre une lampe au mercure à large bande et les LED UV disponibles dans le commerce. La production standard de mercure est représentée par les nombreux pics ombrés verts, tandis que la production de LED UV est représentée par les courbes en cloche violettes plus hautes. Environ un tiers des émissions de mercure se situent dans la région infrarouge (700 nm à 1 mm) située à droite de la bande visible et non représentée sur l’illustration. En revanche, les systèmes LED UV sont dépourvus d’infrarouge, ce qui signifie qu’ils transfèrent beaucoup moins de chaleur totale à la surface de polymérisation que les lampes au mercure classiques. Cependant, les longueurs d’onde ultraviolettes restent une forme d’énergie rayonnée, et une partie de l’énergie UV est finalement convertie en chaleur thermique lorsqu’elle atteint une surface.

Quelles informations importantes ce diagramme d’irradiance spectrale communique-t-il ?
Le graphique d’irradiance spectrale illustre clairement la différence entre la sortie à large bande du mercure (Hg) et la sortie quasi monochromatique de la technologie UV LED à travers les UVC (200 à 285 nm), les UVB (285 à 315 nm), les UVA (315 à 400 nm), Longueurs d’onde UVV (400 à 450 nm) et visible (400 à 700 nm). Deuxièmement, il démontre comment l’ampleur relative de l’irradiance varie en fonction de la longueur d’onde pour les lampes à large bande, ainsi que le fait que des irradiations plus importantes sont possibles avec les LED UV qu’avec le mercure. Enfin, même si les lampes au mercure et les systèmes LED UV émettent de l’énergie UV, il existe clairement des différences significatives en termes de longueur d’onde et d’irradiation qui doivent être prises en compte dans le développement du système, de la formulation et de l’application.
Il convient de souligner que ce tableau est une illustration générale d’une lampe à arc à électrode GEW typique et des systèmes LED GEW disponibles dans le commerce. La répartition de la lampe à arc serait légèrement différente pour un autre produit et sensiblement différente pour une lampe additive. Du point de vue de l’approvisionnement, les LED UV sont fournies et tarifées par les fabricants de semi-conducteurs en fonction de la tolérance de longueur d’onde et de sortie, une tolérance typique étant de ± 5 nm. En conséquence, il y a toujours une légère déviation dans l’empilement des diodes, ce qui affecte le profil spectral et la longueur d’onde à laquelle les courbes des LED culminent. En ce qui concerne les LED, des changements mineurs de longueur d’onde ne produisent généralement pas beaucoup de différence en termes de durcissement. Pour la plupart des applications de durcissement des LED UV, c’est l’ampleur de l’irradiance et la densité d’énergie correspondante à une longueur d’onde de LED UV donnée qui jouent un rôle plus important dans la réticulation.
Comment les diagrammes de sortie spectrale/irradiance sont-ils utilisés dans la pratique ?
Les graphiques de sortie spectrale/irradiance sont un outil principalement utilisé pour comparer différentes lampes de polymérisation ou conceptions de systèmes et les associer correctement aux packages de photoinitiateurs et à la charge de pigment des formulations UV existantes. Les formulateurs et les fournisseurs de matières premières s’appuient également sur des diagrammes de rendement spectral/irradiance pour développer de nouvelles produits chimiques. Toutes les sources UV ne guérissent pas toutes les formulations, et certaines émissions spectrales sont mieux adaptées à certaines applications qu’à d’autres. En effet, les formulateurs sélectionnent parmi une gamme de photoinitiateurs disponibles dans le commerce. Le photoinitiateur est la partie de la chimie qui absorbe la lumière UV et entraîne la réticulation au sein du polymère. Même si les photoinitiateurs absorbent la lumière UV sur une large gamme de longueurs d’onde, un photoinitiateur donné est toujours plus réactif à certaines longueurs d’onde et nécessite un seuil d’irradiation minimum pour s’initier. Différents photoinitiateurs produisent également différentes propriétés esthétiques et fonctionnelles des polymères en fonction de leur conception, de leur réaction avec l’énergie UV et de leur réaction avec le reste de la chimie. Les formulateurs évaluent les courbes d’absorption des photoinitiateurs disponibles par rapport aux graphiques de sortie spectrale et prennent des décisions de compromis et de mélange en fonction des besoins des lignes de fabrication et des presses ainsi que des exigences d’utilisation du produit final.
Pénétration de longueur d’onde pour les systèmes de polymérisation à l’arc d’électrode et aux LED UV
Comme l’illustre l’image suivante, les longueurs d’onde UVA et UVV plus longues pénètrent profondément dans les encres, les revêtements et les adhésifs, tandis que les longueurs d’onde UVC plus courtes sont absorbées à la surface de la chimie. Sur la base de ces informations ainsi que de la puissance spectrale et de l’irradiance spectrale des unités de polymérisation commerciales, les formulateurs recommandent les sources et les types de lampes les mieux adaptés à leurs encres, revêtements et adhésifs. Ces recommandations se présentent sous la forme de spécifications de lampes (mercure, fer, gallium, etc.) ou de préférences de longueur d’onde des LED (365, 385, 395 ou 405 nm). En fin de compte, les formulateurs doivent s’assurer que leurs produits fonctionnent avec une large gamme de systèmes de durcissement UV qui n’émettent pas nécessairement le même rendement, ce qui n’est pas toujours une tâche facile.

Il n’existe pas de source LED UV qui imite directement une lampe au mercure à large spectre, mais les longueurs d’onde plus longues émises par les LED font que la distribution spectrale est plus similaire à celle de la partie supérieure d’une lampe au fer ou au gallium qui émet également une certaine puissance dans le 385 à 405. plage nm. Les LED à 385, 395 et 405 nm ainsi que les lampes dopées au fer et au gallium utilisent toutes des longueurs d’onde plus longues et proches du visible pour pénétrer profondément dans la chimie et produire mieux grâce au durcissement, en particulier avec des formulations plus épaisses, blanches opaques et hautement pigmentées. Pour les revêtements transparents UV LED, obtenir une surface dure, résistante aux produits chimiques et aux rayures, sans jaunissement, a été le principal défi. En effet, la plupart des formulations de revêtement s’appuient sur des longueurs d’onde UVC plus courtes émises par des lampes à large bande pour la réticulation à la surface, et les photo-initiateurs qui réagissent aux longueurs d’onde UV plus longues des LED peuvent jaunir ou se troubler pendant l’exposition. Bien que cette légère décoloration puisse être facilement masquée avec des pigments contenus dans l’encre, elle peut être plus visible avec une chimie claire.
En général, les systèmes LED UV présentent un avantage par rapport aux systèmes conventionnels en termes de durcissement plus profond. Cela est dû à la concentration des longueurs d’onde UVA et UVV ; cependant, les LED UV peuvent avoir du mal à durcir en surface lorsque les formulations ne sont pas optimisées pour les sources émettrices qui n’émettent pas d’UVC. Lorsqu’elles sont mal adaptées, le durcissement par LED UV peut laisser certaines formulations collantes ou grasses au toucher. L’optimisation de la chimie, la sélection appropriée d’une source de LED UV, l’utilisation d’un rayonnement plus élevé et une intégration réfléchie peuvent souvent éliminer les problèmes de durcissement de surface. L’ajout de diodes UVC à un dispositif de polymérisation à LED pourrait finalement s’avérer nécessaire pour les revêtements industriels plus complexes ; Cependant, malgré le fait que les LED UVC entre 275 et 285 nm ont apporté des améliorations significatives en termes d’irradiation maximale, de fiabilité et de durée de vie, la technologie est en retard par rapport à celle des LED UVA et n’est pas encore économiquement viable pour la plupart des applications. La majorité des systèmes de durcissement par LED UV installés et fonctionnant sur les lignes de fabrication aujourd’hui mesurent 395 nm, et la plupart des encres, revêtements et adhésifs utilisés dans les applications d’impression graphique sont conçus pour durcir à cette longueur d’onde.
Irradiance, densité d’énergie et longueur d’onde
L’irradiance, la densité énergétique et la longueur d’onde jouent tous un rôle essentiel dans le durcissement par UV. Premièrement, un niveau minimum d’irradiation à des longueurs d’onde facilement absorbées par le boîtier photoinitiateur doit être délivré à la surface durcie. Dans ces conditions, les photoinitiateurs absorbent l’énergie ultraviolette, génèrent des radicaux libres et conduisent à la réticulation au sein de la chimie. Dans les processus de durcissement UV dynamiques, les queues les plus externes d’un profil d’irradiance en forme de cloche tombent souvent en dessous du seuil d’irradiation minimum et ne produisent pas suffisamment de réticulation au sein de la chimie, mais à mesure que la surface de durcissement se rapproche de la tête de lampe, une irradiation plus appropriée est rapidement obtenue. établi. Deuxièmement, le seuil d’irradiation minimum ou supérieur doit être maintenu pendant toute la durée de la réaction. Enfin, une fois que l’irradiance nécessaire est délivrée et maintenue à la surface de polymérisation, la densité d’énergie devient le facteur déterminant du durcissement et le facteur limitant pour une vitesse de ligne la plus rapide possible ou un temps de cycle le plus court possible. En d’autres termes, la densité énergétique contribue de manière significative à la vitesse maximale de manipulation des matériaux d’une ligne de fabrication et au degré de photopolymérisation pouvant être atteint dans les encres, revêtements et adhésifs UV.
Evolution de la chimie UV
Depuis près de 70 ans, en fonction du marché et de l’application, l’industrie du durcissement par UV a formulé une chimie adaptée aux émissions spectrales des lampes conventionnelles au mercure et dopées au mercure. Toute chimie historique utilise des matières premières spécialement conçues pour répondre aux émissions à large spectre du mercure. Des travaux de développement dédiés à la chimie des LED UVA à bande étroite chez quelques formulateurs ont commencé entre 2005 et 2010. La plupart des industries de polymérisation établies ont cependant retardé leur implication jusqu’à ce que les utilisateurs finaux soient plus intéressés et que la faisabilité et la rentabilité du polymérisation par LED UV se soient améliorées. D’autres formulateurs sont entrés entre 2010 et 2020, et bien d’autres, en particulier dans le domaine des revêtements industriels, commencent tout juste à démarrer à l’approche de 2021. La même chose peut être dite de nombreux fournisseurs de systèmes de durcissement conventionnels qui ont retardé la commercialisation de systèmes LED UV jusqu’à ce que la demande du marché se matérialise.
En général, la chimie UV conventionnellement formulée conçue pour les systèmes de lampes au mercure à large spectre ne durcit pas bien avec des LED UV de longueur d’onde plus longue et quasi monochromatiques. En raison des différences de sortie spectrale, la chimie conventionnelle doit être reformulée pour durcir complètement avec une source LED UV. À mesure que de plus en plus d’entreprises d’encres, de revêtements et d’adhésifs développent des offres de LED UV, elles conçoivent de plus en plus de produits chimiques permettant de polymériser une seule formulation avec des LED tout en étant rétrocompatible avec les lampes à large bande conventionnelles. Ceci est connu sous le nom de chimie à double durcissement et vise à contribuer à réduire les SKU et à faciliter la transition vers la technologie LED UV.
Au cours des années à venir, de plus en plus de formulations auront une capacité de double polymérisation, et les formulations contenant uniquement du mercure seront rendues superflues et finalement abandonnées. Cela ne signifie pas que tout ce qui est historiquement conçu pour les lampes à arc à électrodes disparaîtra demain, car de nombreuses industries, en particulier celles qui utilisent des encres et des revêtements industriels hautement fonctionnels ainsi que celles qui exécutent des profils de pièces 3D complexes et durcissent sur de plus grandes distances de travail, nécessitent des travaux de développement supplémentaires sur les formulations. lampes et intégration. Cette affirmation signifie simplement qu’il est nécessaire de prêter attention à ce qui se passe dans chaque industrie spécifique afin de comprendre l’impact des LED sur les processus de fabrication UV existants. La transition vers les LED UV est en cours ; cependant, il est calculé et progressif en fonction des besoins de chaque industrie et application. Il est essentiel de prêter attention aux besoins en matière de puissance spectrale, d’irradiance spectrale, d’irradiance et de densité d’énergie d’une application pour déterminer si une lampe à arc à électrode spécifique ou un système de durcissement par LED UV spécifique durcira une encre, un revêtement ou un adhésif et quel type de lampe ou longueur d’onde de LED est optimal pour l’ensemble du processus et de la chimie.
1RadTech Amérique du Nord. (2005). Glossaire de termes – Terminologie utilisée pour la conception et la mesure du processus de durcissement aux ultraviolets (UV). Groupe de mesures UV RadTech. pp. 1 – 6. https://www.radtech.org/images/pdf_upload/UVGLOSS_rev4-05.pdf 2Organisation internationale de normalisation.